Medical Technologies
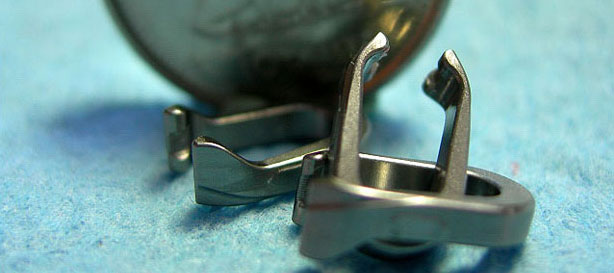
It Takes Firm Resolution To Master The Micro
This shop’s experience of successfully machining a micro aneurysm clip in silicon nitride ceramic points out the need to have CAD, CAM and CNC capability at high resolution—plus the commitment to pull it all together. Article From: MMSOnline.com, Matt...
MANUFACTURER HELPING TO MAKE MEDICAL HISTORY
A small Qualicum Beach business is playing a key role in a major medical advancement that could revolutionize surgical practices. Micro Precision Parts Manufacturing Ltd., already a leader in the ceramic machining industry after just three years of...
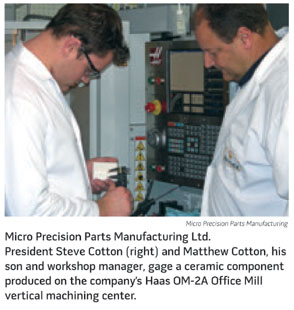
Perfecting a Medical Partmaking Process
From Cutting Tool Engineering Magazine May 2008 MICRO PRECISION PARTS MANUFACTURING LTD., Qualicum Beach, B.C., makes small parts for several applications, including advanced medical applications (see Productive Times on page 118 in this issue for more...
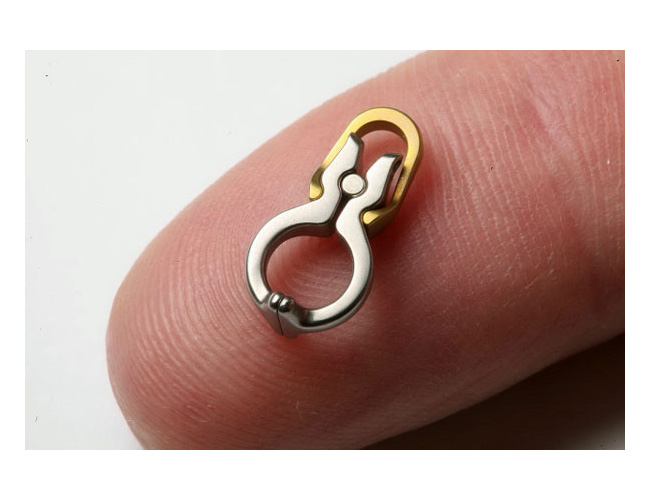
Ceramic Aneurysm Clips
As published in NEUROSURGERY Magazinewww.neurosurgery-online.com Garnette R. Sutherland, M.D.Department of Clinical Neurosciences,University of Calgary,Calgary, Canada John J.P. Kelly, M.D.Department of Clinical Neurosciences,University of...